Cobots in the Food Industry
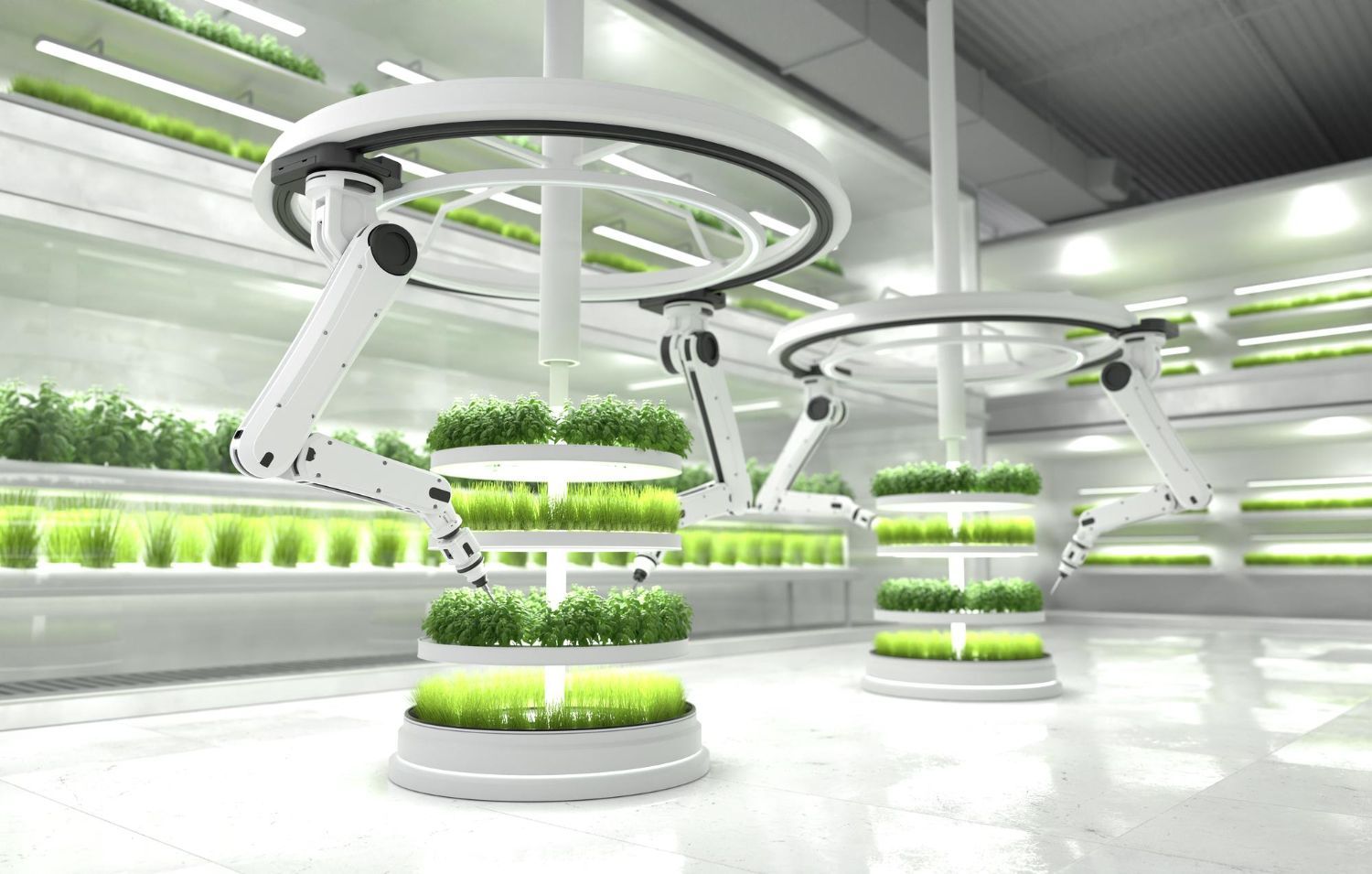
Safety and quality are paramount in the food industry. But with growing demands from over seven billion people, how can the food industry safely increase their production whilst maintaining the quality of their products?
Cobots could be the answer.
Primarily known for cobot welding and logistics, there are plenty of ways to use cobots in the food industry. We’ll explore the transformative impact cobots have in ensuring safety and compliance, while displaying cobot welding excellence within the food industry.
Ensuring Food Safety and Compliance with Cobots
Cobot welding abilities are proving to be invaluable in the food sector. In food processing facilities, equipment is often made of stainless steel. Despite being made of steel, wear and tear can damage the equipment and cause even stainless steel mixing tanks to develop cracks that need welding to prevent contamination risks.
Cobots can be programmed to complete this task with precise and consistent welds, ensuring no contaminants enter the tank during and after the repair process. Additionally, cobots can potentially be programmed to conduct safety checks to ensure compliance of the equipment with food safety regulations. Using cobots, production facilities can maintain food safety compliance while minimising the risk of human error.
Cobots in Food Processing and Packaging Operations
Conveyor belts are a common feature in food packaging operations: they transport products for processing and eventually for delivery to the consumer. But even these belts can suffer wear and tear over time and may require welding for repairs.
Cobots equipped with welding tools and sensors can detect and efficiently repair any damage it finds in the belts. By employing cobots in the food industry, food manufacturers can maintain the efficiency of their operations, ensuring that products continue to move smoothly through the packaging process, reducing downtime and disruptions to critical processes.
Cobots for Automated Inspection and Quality Control
Like most industries, equipment and tools used in the food industry are fabricated through complex processes including forging and welding. After the welding process, cobots use its sensors and cameras to inspect the welds meticulously. Subpar welds are then flagged for human review or rework.
Cobots in the food industry can be programmed to autonomously identify defects, inconsistencies, and weld quality issues, upholding safety and quality standards.
Successful Implementation of Cobots in the Food Industry
With an industry as highly regulated as food production, implementing cobots effectively requires careful planning and expertise to be successful. When done correctly, cobots can be the driving force to support the growing needs in the food industry across the globe.
As the food industry continues to evolve and needs continue to grow, cobots are poised to become indispensable allies in this sector. By embracing this technology and understanding the importance of cobots in the food industry, businesses can potentially meet then exceed their production goals, setting new standards for excellence and safety in the food industry.
Are you a forward-thinking business owner looking to enhance your production processes and stay competitive in today’s rapidly evolving landscape? Cyber Weld’s team of experienced robot systems integrators are ready to help.
Contact us today to explore how cobots can revolutionise your production processes and lead your business into a new era of efficiency and productivity.