Choosing the Right Cobot Welding System
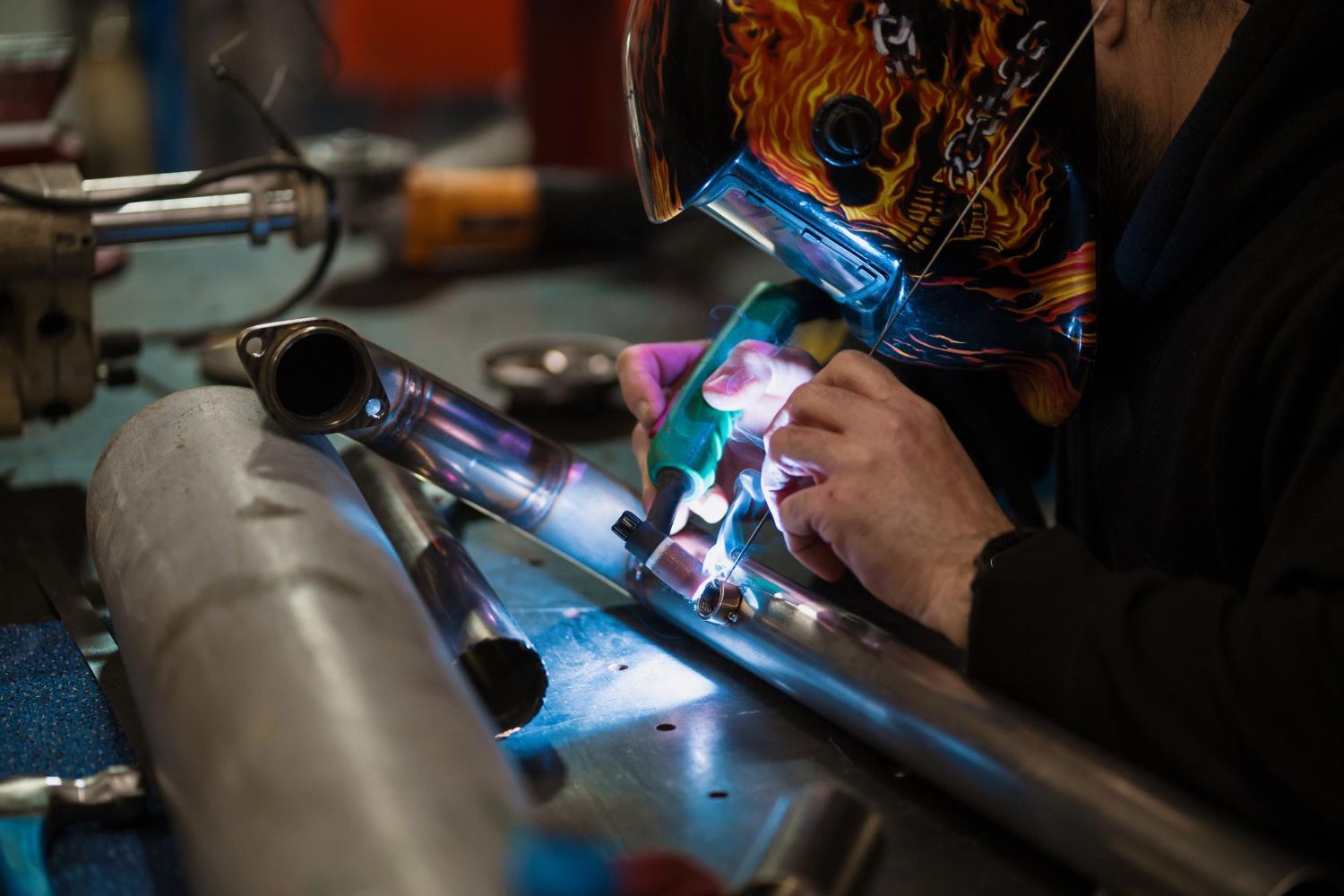
Cobot welding systems are the future in the manufacturing industry. They offer numerous advantages for adopters through increased productivity, improved safety, and greater flexibility.
But with the range of cobot systems available, it can be challenging to decide which cobot is the most suitable for your needs. In this article, we’ll explore key factors to consider when choosing the right cobot welding systems for your business.
Evaluating Your Requirements
The first step in selecting suitable cobot welding systems is to evaluate your application requirements.
Consider the materials being welded. How complex or simple are they? What’s the production volume? Different cobots are geared to excel at different tasks.
What’s Your Budget
Before picking a cobot welding system, bear in mind costs can fluctuate based on the features and capabilities of the system you choose.
It might seem appealing to choose the most economical cobot system upfront, but consider the long-term perspective. Besides the initial investment, factor in potential future requirements for scaling your systems. Even if the system seems perfect today, if your demands increase in the near future, a poorly chosen system may lack the scalability to accommodate growth, leaving you with no choice but to replace it entirely rather than a simple upgrade.
Key Factors to Consider
What are the technical specifications to look for when choosing a cobot welding system? It’s important to carefully scrutinise technical specifications to ensure they align with your operational needs. Some areas you should evaluate include:
Payload capacity
Can the selected cobot welding systems handle the combined weight of the welding torch, cables, and any additional tooling your application requires? Inadequate payload could hinder productivity, performance and compromise safety.
Reach
Ensure the cobot system has enough reach to not only accommodate the size and dimensions of your products, but also perform welding operations from all the necessary positions and angles. Certain cobot systems may have restricted reach capabilities, leading to limitations in how and where they can be effectively utilised.
Accuracy and reliability
Carefully consider your application’s accuracy and repeatability requirements. If your welding tasks demand extremely tight and consistent, precise results, opt for a precision or dexterous cobot welder. Conversely, if your welding operations involve larger structural components, heavy equipment fabrication, or applications where weld integrity is more important, an industrial-grade cobot welder may better suit your needs.
Welding process compatibility
Your welding process requirements will help you determine which system has the best compatibility with your needs. Whether you utilise MIG, TIG, spot welding or other techniques, the cobot must integrate those processes natively without needing costly workarounds. Some cobot welding systems are dedicated for certain processes, while others offer flexibility across multiple methods. Opting for an incompatible system may require expensive retrofitting and could undermine the cobot’s performance.
Additional Factors to Weigh
Beyond the technical specifications above, several other key factors such as safety, user-friendly systems and ease of maintenance must also be considered. User-friendly systems with intuitive programming interfaces and easy operation can simplify training and minimise downtime.
Since cobots work alongside humans, any system chosen should have robust safety features like force-sensing and emergency stops. Furthermore, consider the vendor’s training and support offerings, like documentation, tutorials and availability of local service technicians for maintenance.
Cobot welders require ongoing maintenance like cleaning, calibration and regular inspections, so convenient access to the manufacturer’s technical support and service team is vital for long-term usability. Accounting for user experience, safety, and vendor support along with performance specs ensures selecting a cobot welder aligned with your operations.
Ready to Improve Your Manufacturing Capabilities Using Cobots?
Cyber-Weld can help. Our team of experts are ready to guide you through the selection process and help you find the perfect cobot systems to streamline your welding operations, boost productivity, and drive your business forward. Contact us today to schedule a consultation and experience the future of welding automation.