Advanced Cobot Welding Solutions
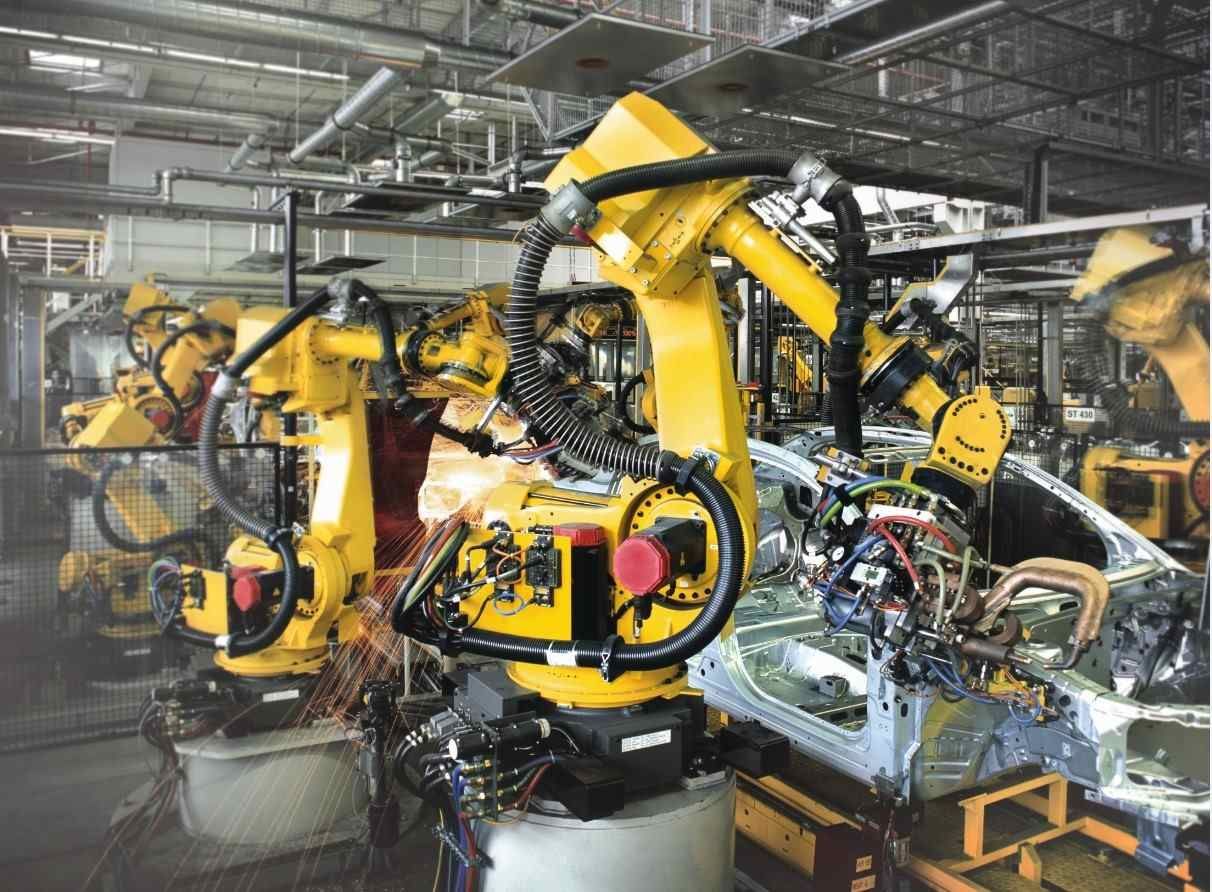
Precision, efficiency, and safety are key features of any manufacturing industry. These factors increase the productivity and, as a result, the overall profit of any business.
But how can a smaller business compete against larger companies that have both the space and budgets to integrate advanced and heavier machinery? One such technology that has gained significant traction and is giving early adopters a competitive edge in advanced welding solutions is cobot welding. Cobot solutions combine the precision of robotics with adaptability and safety.
At the core of it, cobot welding systems are designed to work seamlessly alongside human operators, offering a unique synergy between automated processes and human expertise. These cobot solutions leverage cutting-edge technologies to deliver superior results while prioritising safety and flexibility. We’ll explore the key features of advanced welding solutions and how they can improve precision, efficiency, safety and the bottom line of your business.
Precision and Accuracy
Precision and accuracy are crucial in welding operations, as even minor deviations can lead to defects, rework, and scraps that can severely affect profits.
Using advanced sensor technology and vision systems, cobots continuously monitor and adjust their movements, ensuring consistent and high-quality welds compared to traditional industrial robots. This level of precision improves the overall quality of your final product and reduces the need for rework and material waste.
In contrast, traditional industrial robots, while precise and powerful, often lack the ability to dynamically adjust their movements based on real-time feedback. They rely heavily on pre-programmed trajectories, which can be affected by environmental factors or changes in the workpiece positioning.
Enhanced Safety
Safety is another critical concern in any manufacturing environment. There have been many incidents in the past where traditional industrial robots have been involved in small and major accidents.
Cobot solutions excel here. These advanced welding solutions have force-limiting and safety monitoring systems to detect potential hazards and respond accordingly, minimising the risk of accidents and ensuring a safe working environment for human operators.
Traditional industrial robots, while capable of performing welding tasks, pose a significant safety risk when operating in close proximity to human workers. They require extensive safety measures, such as physical barriers or fenced-off areas, to prevent accidents.
On the other hand, cobot solutions are designed to work collaboratively with human operators, enabling seamless interaction and task sharing. This enhances overall efficiency, productivity and fosters a safer work environment, reducing the need for physical barriers.
Flexibility and Adaptability
Another key advantage of cobot solutions is their flexibility and adaptability.
With a wide range of options and advanced welding solutions, cobots can be easily reconfigured to handle diverse welding applications, accommodating evolving manufacturing demands with ease.
Traditional industrial robots are often designed for specific tasks and may require significant reprogramming or reconfiguration to adapt to new applications or product changes. This can lead to costly downtime and manufacturing delays.
Because cobot solutions, on the other hand, can be quickly adapted to new tasks or product variations, you can expect minimal disruption to your manufacturing schedule. Their advanced programming capabilities allow for easy integration of new welding processes or modifications to existing ones, enabling manufacturers to respond rapidly to changing market demands or customer requirements.
The flexibility and adaptability of cobot solutions not only improve operational efficiency but also provide a competitive advantage by enabling faster time-to-market for new products or variations.
Benefits of Implementing Advanced Cobot Welding
By now you know cobot welding systems are a combination of precision, intelligence and adaptability, but what are the actual benefits of integrating them into your manufacturing cycles?
When you leverage the latest advanced cobot solutions which make use of technological advancements in sensor technology, vision systems, and programming capabilities, these cobots deliver unparalleled benefits to your welding operations.
Here are some benefits you can expect when you integrate cobots into your business.
Accelerating Productivity and Efficiency
Faster Welding Processes: Cobots work tirelessly and consistently, significantly increasing welding output and reducing cycle times. With unwavering focus and precision, cobots streamline welding processes and maximise output and productivity.
Reduced Downtime: Built with robust construction and equipped with preventive maintenance capabilities, cobot welding systems can minimise unplanned downtime. Less downtime maintains maximal operational efficiency, saving your business from costly disruptions.
Uncompromising Quality and Consistency
Consistent Welding and Minimised Defects: Poor weld quality, defects and reworks costs you both in profits and reputation. Cobots leverage advanced sensor technology and sophisticated programming to deliver consistent and repeatable weld quality.
Enhancing Collaboration and Skill Augmentation
Human-Cobot Interaction: Designed to work collaboratively with human operators, cobots have built in features that enable seamless interaction and task sharing.
Skill Augmentation: Human operators can offload repetitive and physically demanding tasks to cobots, allowing them to focus on higher-level skills, such as programming, quality control, and process optimisation.
If you’re looking to integrate cobot solutions into your manufacturing operations, Cyber-Weld is ready to help. We understand the importance of staying ahead in the manufacturing landscape and our team of dedicated experts can help your business harness the power of advanced welding solutions.
Schedule a call with us to find out how we can help you achieve unparalleled levels of precision, efficiency, and safety in your manufacturing operations.