Robots can be used for a wide range of material handling tasks across numerous sectors in the UK and abroad. They’re capable of safely handling, moving and manipulating anything from large, cumbersome weights to small, fragile objects. Material handling robots can be programmed to move, hold or work on materials, components or goods with millimetre accuracy.
A handling robot normally has a versatile, industrial robotic arm. The robot can be dressed with a variety of end-of-arm handling attachments, such as mechanical grabbers, magnets or pneumatic tools, for any number of material handling tasks (transferring parts between conveyor belts or end-of-line palletising, for instance).
Palletising robots are some of the most extensively used handling robots. They exemplify the transformative effect robotic material handling systems have on businesses’ activities. What was once a labour-intensive, dull, time-consuming manual task – stacking goods on pallets, ready for transportation – can now be automated and completed with superb efficiency.
Adding a robot handling system to your factory or warehouse, for example, is an ideal way to introduce automation
or build on existing automation and streamline operations. Imagine what a huge difference palletising robots or another kind of handling robot could make to your business, particularly in relation to boosting your productivity and quality levels.
The Cyber-Weld technical team has years of experience with robotic handling solutions. We can design, build and implement a bespoke robot handling system to handle any object over any distance. We can also integrate that system with your existing technology for a seamless transition. Simply contact us
to discuss your requirements.
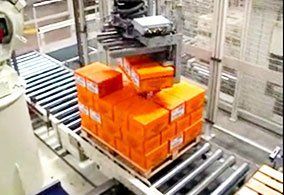
What Is a Robot Handling System?
A robot handling system is an automated, computerised operational solution that employs at least one handling robot to complete or assist employees with specific, repetitive material handling tasks safely, accurately and efficiently. A robot fitted with an appropriate end-of-arm tooling attachment can be programmed to pick up, carry, label, palletise, etc.
Combining hardware (such as robotic arms and controllers) and programming software, robotic handling systems can enhance any stage of production or distribution. You can think of such a system as the central point of control for robotic handling activities. The tasks it’s responsible for are normally carried out in one particular building or between that building and a vehicle (between a storage unit and lorry, say).
Robotic material handling systems are increasingly found in industrial and commercial settings. They’re crucial to many companies’ manufacturing processes
in a wide range of industries. In addition, robotic handling has a major role to play with regards to packaging and packing
goods.
It’s important to emphasise that material handling is an extremely broad, complex area. It’s not just about getting objects from A to B on the factory floor. According to the Material Handling Institute, material handling encompasses all activities related to ‘the movement, protection, storage and control of materials and products throughout manufacturing, warehousing, distribution, consumption and disposal’.
As a result, there’s no such thing as a one-size-fits-all, universal robotic handling solution. All the robotic material handling systems the Cyber-Weld team create and implement are tailored to our customers’ particular needs and facilities.
What Are the Major Applications of Robotic Handling?
Robotic handling can be put to all sorts of uses, and this is reflected in the diversity of the organisations that have adopted the technology. Robot handling systems are particularly common in the automotive, aerospace, agricultural, food and drink, electronics, chemicals, manufacturing, pharmaceuticals, logistics, and retail industries.
Major robotic handling applications include:
- Moving challenging materials – robots handle delicate, unwieldy or hazardous items with ease.
- Part transfer – by efficiently conveying parts from one area to another, a handling robot helps to optimise production processes.
- Machine loading/unloading – supplying machinery with materials or components, such as screws, is a key robotic handling task.
- Conveyor belt loading/unloading – robots keep the production line moving.
- Securely holding parts – this enables employees or machines to work on them.
- Dispensing glue, sealant or paint – a handling robot can do this consistently well.
- Machine tending – robotic material handling systems operate industrial tools, performing tasks such as moulding, milling or painting.
- Product assembly – you can automate jobs such as gluing or welding parts together.
- Harvesting crops – sensors enable the robots to tell which ones are ready to be picked.
- Quality control – robots can thoroughly test and inspect items.
- Pick and place – selecting objects and depositing them in the desired place. Pick and place robots often assist warehouse staff.
- Packing – robots commonly fill trays, assemble boxes and shrink-wrap products.
- Palletising/de-palletising – palletising robots stack items on pallets and unpack recently delivered supplies.
In a nutshell, installing robotic material handling systems is ideal when there are difficult, dangerous, tiring, lengthy or monotonous jobs to be done. Material handling robots can step in to relieve employees of tasks they find nerve-wracking, unappealing or tedious. What’s more, the robots perform such tasks to a consistently high standard.
What Are Palletising Robots Used For?
We’ve highlighted the importance of robotic palletisation a couple of times so far. Introduced in the 1980s, it’s one of the most well-established, popular robotic handling solutions. Indeed, palletising robots play such a vital role in end-of-line operations that it’s worth exploring what they’re used for in detail.
Palletising robots excel at picking up, manipulating and stacking objects – typically products being prepared for transportation – on pallets. They arrange items in patterns and layers and create uniform pallet loads that can be moved by forklift or pallet jack. They can handle sacks, bales, crates and bags too.
Additional tasks performed by palletising robots include placing empty pallets on staging platforms, sorting and packaging products, wrapping pallet loads and de-palletising (i.e. unstacking pallets when you receive deliveries).
When fitted with grippers, suction cups or other end-of-arm attachments, they can handle all kinds of objects without dropping or damaging them. And thanks to their mechanical precision and agility, palletising robots achieve a faster cycle time than is possible by hand. Plus, they never get tired, injured or need breaks. Payload capacities in excess of 1,000 kg aren’t uncommon, and there are even palletising robots built to withstand extreme temperatures (ideal for cold storage units, say).
The video below features one of Cyber-Weld’s impressive robotic material handling systems, Champs, and shows how successfully robots perform end-of-line palletisation.
Champs
We’re proud to produce simple, cost-effective EOL robotic palletising solutions. Our turnkey EOL offering includes the ability to interface with existing equipment for maximum convenience.
Our robotic palletising systems benefit from:
- Vacuum and mechanical gripper technology
- Layer sheet and pallet-handling options
- User-friendly HMI, which interfaces with the PLC (the computer controlling manufacturing processes) to cater for various products
- Compatibility with pallet dispensers and conveyors
Why not contact us
to discover how palletising robots can strengthen your operations?
Which Technology Is Used for Material Handling?
Cutting-edge, adaptable handling robots are at the heart of today’s material handling processes.
Key types of material handling robots include:
- SCARA robots – Selective Compliance Assembly Robot Arms emulate human arm movements. Compact, sturdy and speedy, they excel at small, precise tasks, such as product assembly and inspection.
- Cylindrical robots – by rotating and extending/retracting, they can perform small, straightforward handling tasks, including packaging and machine loading.
- Cobots – collaborative robots work closely with people, usually on assembly lines. Agile and flexible, they’re great at holding parts steady and part finishing.
- Delta robots – they have three slender arms and work at high speed, so they’re an excellent choice for light pick and place, packaging and food processing tasks.
- Cartesian robots – with the ability to move up, down and horizontally and lift heavy loads, they make reliable palletising robots.
- Six-axis robots – their superior range of movement (they can position their arms at almost any angle) gives them fantastic dexterity and reach. Plus, they can handle very heavy loads (over 1,500 kg in some cases). So they’re ideal for complex, challenging activities, such as machine tending and palletisation.
Cyber-Weld has the engineering capability to utilise all robot OEM’s products. We work with the manufacturers of industry-leading technology for robotic material handling systems, including FANUC, ABB, Motoman and Panasonic.
We use 3D CAD and simulation software to design and test robot handling systems in order to ensure they’ll do exactly what you require.
Advantages of a Material Handling Robot
Robotic handling systems are designed to give you the competitive edge. Let’s explore some of the most compelling advantages and benefits of using a material handling robot.
- Enhanced safety – robots reduce the risk of accidents and contamination by reducing the need for human intervention.
- Increased productivity – robots work continuously and are reliable, precise, quick and versatile. They make operations more efficient even when pinpoint accuracy is required, so you can enjoy faster cycle times and more consistent results.
- Highly engaged employees – automation leaves them free to focus on stimulating tasks.
- Greater customer satisfaction – a robot handling system helps you to improve quality, minimise errors and meet demand.
- Reduction in labour costs – one handling robot does the work of multiple people and needs little space (ideal if you run a tight ship).
- Fast ROI – robots enable you to save money on wages, boost your productivity and decrease waste, so they’re soon paying for themselves.
Robotic Handling and Palletising Experts
To find out how robotic material handling systems can enhance your business, contact Cyber-Weld
today.