The Role of AI and Machine Learning in Cobot Welding
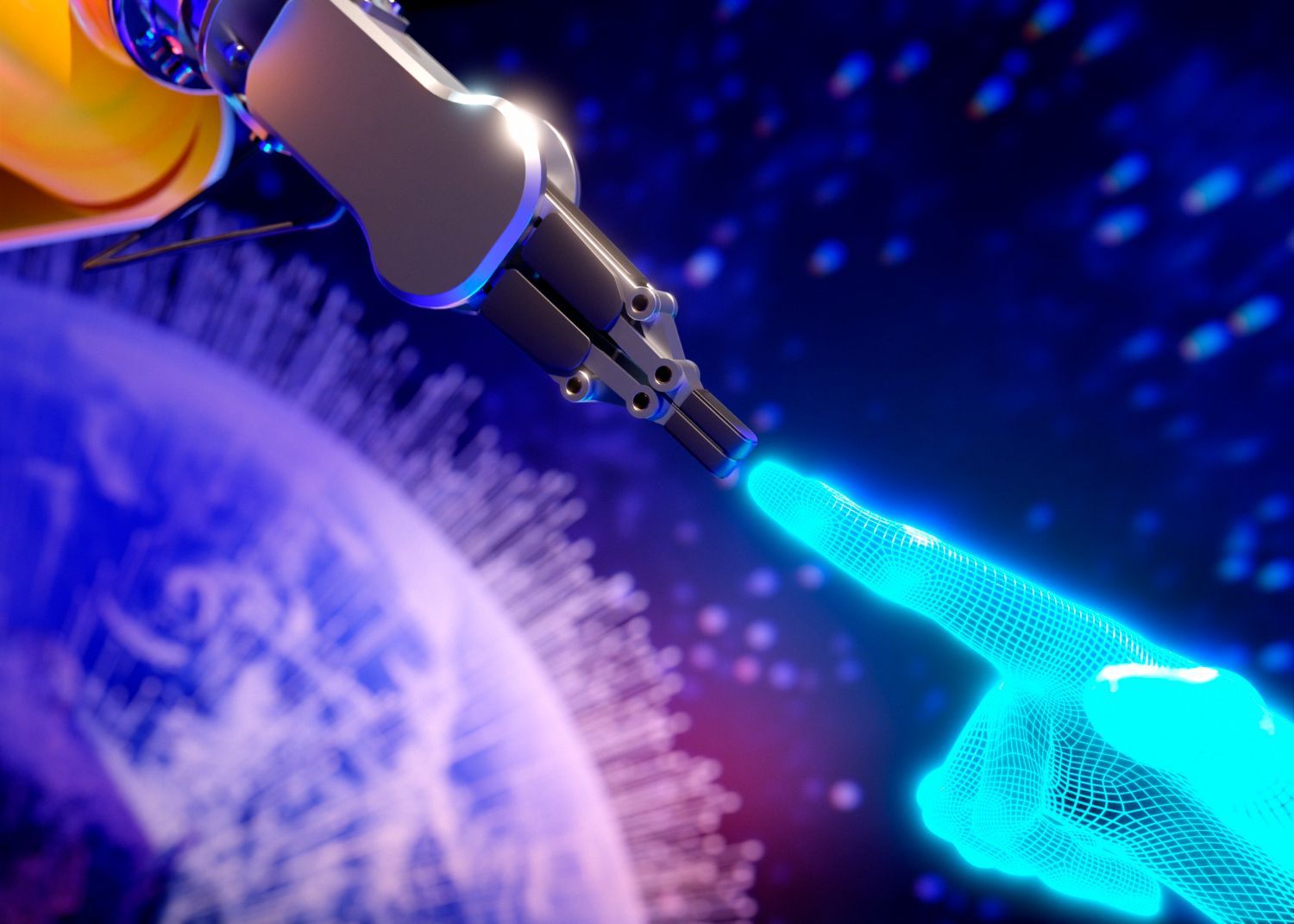
The automation of manufacturing industries is inevitable. With the integration of artificial intelligence (AI) and machine learning (ML) in almost every industry, it’s beneficial for manufacturing companies to adopt this technology sooner rather than later.
Especially in the realm of welding where collaborative robots, or cobots, are already revolutionising the landscape. From precision welding, to welding in hazardous environments, cobots are filling, taking on roles and reducing risks for their human counterparts.
But how will AI and ML affect the landscape of cobot welding? What is their impact on precision, efficiency, quality control on welds, and on training and skill development for human workers?
Understanding AI and Machine Learning in Cobot Welding
ChatGPT stands out as a widely used application of AI and ML today. Using patterns and information present in the data it was trained on, this AI does everything from writing social media captions to full-blown academic essays.
But how does AI in welding work?
Cobots are blank slates. Like human operators they need to be trained before they can perform their designated tasks. By using recorded data and past welding patterns, cobots can be trained much quicker than human operators to equip them with the necessary abilities to adapt to their roles. By integrating AI and ML in cobots, not only is the time taken to train new cobots significantly reduced, they can adapt rapidly to various situations and make autonomous decisions on their own.
Increased Precision and Efficiency
Another key advantage of incorporating AI in welding when using cobots is the precision and efficiency they bring to the manufacturing process.
Traditional robotic welding systems struggle to adapt to unexpected changes in the work environment, as they are subjected to the efficiency and ability of their human operators. This can lead to inefficiencies and delays in the production line and can cost the company its revenue.
AI welding cobots can analyse real-time data, adjust their parameters, and seamlessly adapt to variations in the welding environment.
Unlike traditional robots, the adaptability of cobots to seamlessly accommodate and switch between the diverse welding patterns often encountered in various production lines such as T-joints, fillet welds, and groove welds is one of their greatest advantages. This adaptability not only elevates the precision and quality of welds, but also enhances overall efficiency in your production processes.
Improved Quality Control
Quality control is one of the most critical aspects of welding. AI and ML can play a pivotal role in it by minimising defects and ensuring superior weld quality in all your products.
Through continuous monitoring of welding parameters, AI-driven cobots can detect deviations in production. This proactive approach allows for real-time adjustments, reducing the amount of defects, scrap, and rework. You’ll find significant improvement in overall quality and a reduction in defects of welding projects. Lower amounts of reworks will ultimately result in a lower amount of scrap and an increase in cost savings for your business.
Safety Enhancements
Safety is important in every manufacturing environment. But with the presence of AI and ML, safety risks and accidents in cobot welding environments are significantly reduced.
AI-driven cobots are equipped with advanced sensors and vision systems that enable them to detect and respond to the presence of humans or obstacles in their vicinity. This allows them to work safely alongside their human operators and create a safer working environment by preventing collisions, reducing the risk of injuries.
Training and Skill Development
As cobot welding becomes more prevalent, the need for skilled workers capable of operating and maintaining these advanced systems is on the rise. AI and ML technologies are not only transforming the manufacturing process but also influencing the way workers are trained. Virtual reality simulations, powered by AI, provide a realistic and interactive training environment for welders to familiarise themselves with cobot welding systems. This approach accelerates the learning curve, improves skill development, and prepares workers for the evolving landscape of automated manufacturing.
Future Trends in AI and Machine Learning for Cobot Welding
What’s next for cobot welding?
With the integration of AI and ML, cobot welding is poised to witness further advancements such as predictive maintenance, where AI algorithms anticipate equipment failures and schedule maintenance proactively, or the integration of collaborative learning systems that allow cobots to share knowledge and experiences with each other, creating an interconnected and intelligent manufacturing ecosystem.
As the technology evolves, and machine learning welding software continues to improve, the future of cobot welding will likely be characterised by even greater efficiency, precision, and adaptability.
From increased precision and efficiency to improved quality control and safety enhancements, the impact of this technology is far-reaching. As the manufacturing industry continues to embrace automation, the synergy between human expertise and AI-driven cobots will shape the future of welding, creating a more efficient, safe, and technologically advanced landscape.
Isn’t it time your business experienced the advantages of a cobot-welding package?
Cyber-Weld’s specialised team will deliver a tailored package that will make your welding operations outshine your competitors. Reach out today and let us tailor a package for you.