Collaborative Robots: An Overview
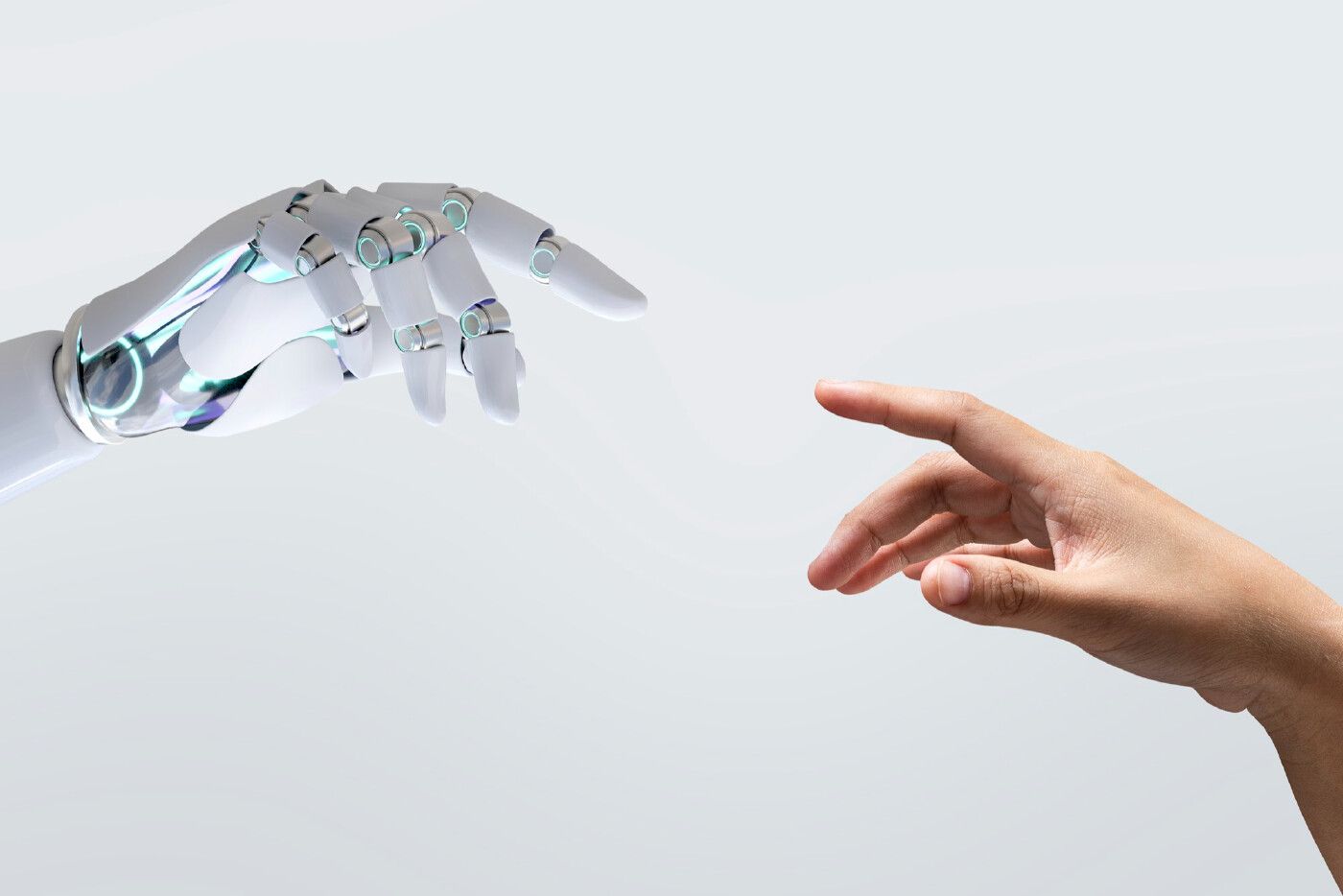
In recent years, cobot welding has gained significant attention in the manufacturing industry.
Collaborative robot welding, also known as cobot welding, revolutionizes the way welding tasks are performed. With the advancement of technology, cobot welders have emerged as a safe and efficient alternative to traditional welding processes.
These intelligent machines are designed to work alongside human operators, assisting them in various welding applications. By combining the precision and strength of robotic systems with the dexterity and decision-making capabilities of human workers, cobot welding offers enhanced productivity, increased flexibility, and improved overall safety in welding operations.
Cobot welders can perform repetitive and labor-intensive welding tasks with high accuracy, while their collaborative nature ensures a harmonious and efficient workflow between humans and robots.
Collaborative robots, known as cobots, have emerged as a game-changer in the world of robotics. Unlike their traditional counterparts, these robots have been designed to be safer for use alongside people, opening a realm of possibilities for human-robot collaboration.
Cobots are becoming increasingly popular due to their many advantages over traditional industrial robots. They are safer, more flexible, and more affordable than their traditional counterparts. In addition, the ease in which they can be programmed and operated makes them a good choice for businesses of all sizes.
Types of Collaborative Robots
There are four main types of collaborative robots:
Power and Force-Limited Cobots
Power and force-limited robots are the most common type of collaborative robot. They’re designed to stop if they encounter a human. This is done by limiting the amount of force the cobot can exert. Power and force-limited robots are typically used in applications where there’s a risk of human-robot contact, such as assembly and manufacturing.
Safety-Monitored Stop Cobots
Safety-monitored stop robots are similar to power and force-limited robots, but have additional sensors that can detect human presence. If a human is detected, the robot will stop until the human is clear. Safety-monitored stop robots are typically used in applications where there’s a high risk of human-robot contact, such as painting and arc-welding robots.
Hand-Guided Cobots
Hand-guided robots like collaborative arc welding robots are controlled by a human operator. They’re equipped with a hand-guided device that allows an operator to directly control the robot’s motion during automatic mode. In this mode, the robot responds to the operator’s direct control input, ensuring precise manipulation of heavy workpieces while reducing the risk of repetitive-stress injuries for the operator. Hand guiding as a collaborative operation occurs during normal production in automatic mode, distinguishing it from programming, which is not done during production or in automatic mode. With hand guiding, operators can achieve a higher level of control and safety while working alongside the robot in a collaborative environment.
Speed and Separation Cobots
While similar to safety-monitored stop collaborative robots, these cobots incorporate advanced vision systems that enable them to automatically slow down operations when a human worker approaches and even completely halt the operation when a worker gets too close. By prioritising speed control and maintaining a safe distance, speed and separation collaborative robots ensure a safe working environment for humans and robots.
Applications of Cobots
Collaborative robots have emerged as a game-changer in various industries, revolutionising the way tasks are performed. With their ability to work alongside humans in a safe and efficient manner, cobots are finding their place in a multitude of applications, unlocking new possibilities across different processes.
Manufacturing
Collaborative robots excel in a wide range of manufacturing processes. Their precision and efficiency make them valuable assets in welding and perfecting on the production line.
In arc welding, cobots can be programmed to weld a variety of different joints with extreme precision and accuracy.
A collaborative robot can also be programmed to paint products and will finish the job perfectly. Using cobots for paint jobs reduces the risk of human error, which often leaves imperfections on the final product.
Assembly
Smaller objects in a production line require extreme dexterity that human workers may lack. Cobots can be programmed to handle anything from tiny objects to heavy, larger objects that require significant strength.
Whatever the size of products in production, cobots can be used to assemble it flawlessly. All they need is a program and they can easily follow complex assembly instructions. This makes them ideal for tasks such as assembling electronic devices, medical devices, and appliances.
Compared to humans, they are faster, more accurate, and more consistent. And businesses can expect a significant increase in productivity because cobots don’t tire out.
Packaging
In the realm of packaging, cobots have exceptional capabilities – they can streamline loading, unloading, labelling, and sealing processes with unparalleled speed and precision. This heightened efficiency not only translates to substantial cost reductions but also optimal productivity in packaging operations.
Additionally, they can operate flawlessly in hazardous environments and handle challenges posed by high temperatures or dangerous fumes. By integrating cobots into packaging workflows, businesses can maintain productivity without endangering their own human capital.
Collaborative Robots in Logistics
Cobots equally dominate the logistics landscape; from end-to-end there is always a process that can improve by integrating cobots.
Efficient loading and unloading of trucks, seamless sorting and placement are just two of the ways you can integrate cobots into a logistics team. By integrating cobots into operations, businesses can improve efficiency, delivery times and most importantly customer satisfaction.
While cobots are surely gaining popularity in the UK, integrating them into existing production systems still requires careful planning and execution. As with all new technologies, there are measures and restrictions required to be set in place to ensure the safety of everyone involved.
Integrating Cobots
Choose the Right Cobot
The type of cobot chosen for a business will depend on its specific application. Power and force-limited robots are great options for safe and easy-to-use cobots. If a business is looking for a robot that can detect human presence and stop when necessary, a safety-monitored stop robot may be a better option. But if human input is needed, a hand-guided cobot will serve as the best option.
Plan the Workspace
After selecting a cobot, the next step is to plan the workspace effectively. First, it’s important to allocate sufficient space for the cobot to operate. Cobots require room to move, reach, and perform their assigned tasks without any obstructions. Consider the range of motion and reach of the cobot’s robotic arm, considering both horizontal and vertical movements.
Once you have a space selected, implement appropriate safety measures. This is necessary to prevent accidents or injuries. Safety measures can include installing safety barriers, sensors, or visual indicators to demarcate the cobot’s working area and alert human workers to maintain a safe distance.
Integrate with Existing Systems
One of the significant advantages of cobots is their ability to integrate with existing machinery and equipment. Integration not only enhances overall efficiency but also allows for a more streamlined and coordinated workflow. However, it’s important to consider compatibility and safety aspects when integrating cobots into existing systems.
Ensure that the cobot chosen is compatible with current machinery and equipment. Assess the communication protocols and interfaces to ensure smooth data exchange and interaction between the components of a production line. Consult with cobot manufacturers or system integrators to ensure compatibility and determine any necessary adaptations or modifications that may be required. Most importantly, conduct a thorough risk assessment to identify potential safety hazards that may arise from the cobot’s interaction with other systems or human workers.
Train employees
As cobots are introduced into a production team, it’s essential to provide comprehensive training to the human workforce. Equipping employees with the necessary knowledge and skills will enable them to work safely and effectively alongside cobots, ultimately improving the productivity and maximising the benefits of this technology.
Start by educating employees about the purpose and capabilities of cobots. Then familiarise them with the specific tasks cobots will be performing and how they will interact with the robots in the process.
Missing any of these considerations can result in inefficient production, accidents or even injury. If you’re planning to integrate cobots into your production line, hiring a team of professionals to handle this can save you time and unnecessary costs.
Advantages of Collaborative Robotics
Cobots offer significant advantages over traditional industrial robots. They prioritise safety by minimising the risk of accidents and injuries. Designed to detect human presence and react accordingly, cobots have more advanced sensors to ensure a secure working environment. This allows for closer collaboration between humans and robots.
Another advantage of cobots is their affordability. Thanks to technological advancements and market competition, cobots have become more accessible and cost-effective. Businesses of all sizes can now harness the benefits of automation, empowering smaller enterprises to improve productivity and competitiveness.
It goes without saying that cobots can enhance efficiency and productivity. With consistent performance, cobots optimise operational efficiency and increase production output. Moreover, their adaptability and ease of reprogramming enable businesses to quickly adjust to changing production needs, staying ahead in dynamic industries.
The Future of Collaborative Robotics
The future of collaborative robotics today is being shaped by two transformative technologies: AI and machine learning (ML). These technologies are revolutionising the capabilities of cobots and driving their efficiency to new heights.
AI empowers collaborative robots to learn from their surroundings and adapt their behaviour accordingly. This enhances their decision-making skills, allowing them to perform tasks with greater precision and efficiency.
ML complements AI by enabling cobots to analyse vast amounts of data and make predictions based on patterns and trends. With ML, cobots can autonomously carry out complex tasks, leading to increased productivity and improved performance.
In addition to AI and ML, the field of human-robot interaction (HRI) is a critical area of research. HRI focuses on creating seamless collaboration between humans and robots, ensuring effective communication, safety protocols, and optimised workflows. Advancements in HRI will redefine the dynamics of human-cobot teamwork, unlocking new levels of productivity and efficiency.
As these technologies continue to evolve, we can expect even greater efficiency and productivity gains in industries that embrace the power of cobots.
Collaborative robots are a ground-breaking technology that’s revolutionising industries across the globe. Advances have not only increased their safety but also improved their efficiency and productivity in manufacturing. With their adaptability and ease of reprogramming, businesses can quickly adjust to changing production needs, ultimately enhancing overall productivity.
Ready to unlock the potential of collaborative robots in your production? Cyber-Weld provides a comprehensive range of robotic services, including designing an extensive array of bespoke robotic systems intended for the computing and electronics industry.
Contact Cyber-Weld now to learn how you can effectively implement and integrate cobots into your manufacturing processes.