Cobots vs Industrial Robots: What Are the Differences?
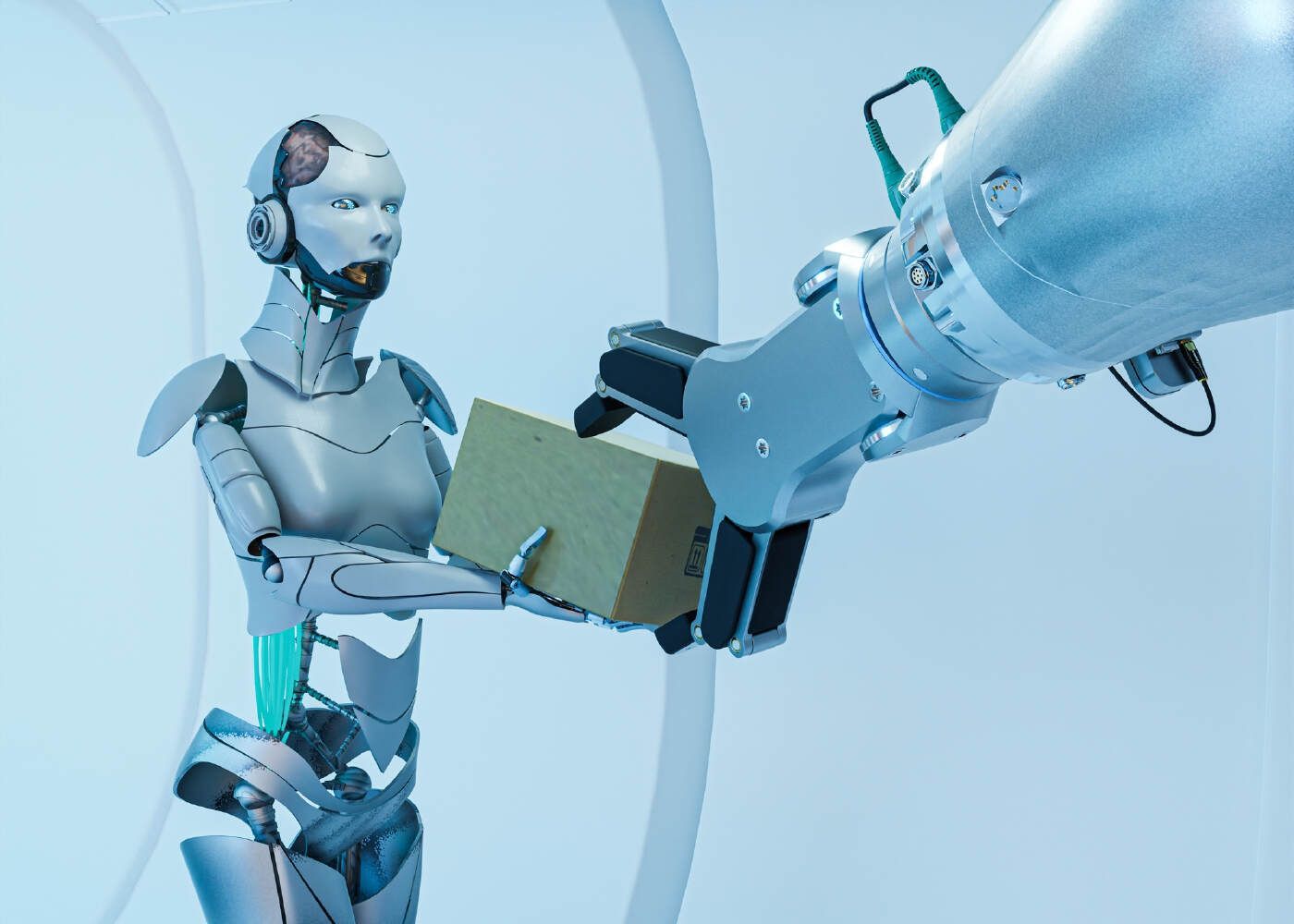
In the realm of automation, cobot welding and collaborative robot welding have emerged as two prominent technologies, each with its unique characteristics.
Understanding the differences between cobots and industrial robots is crucial for businesses seeking to harness the power of automation in their operations. While both cobot welding and industrial robot welding share similarities in their objective of automating welding tasks, they differ in terms of their design, capabilities, and applications.
Collaborative robot welding, or cobot welding, focuses on creating a harmonious interaction between humans and robots, emphasizing safety and collaboration. Industrial robots, on the other hand, are typically larger and more powerful machines designed for repetitive and heavy-duty welding tasks.
In this article, we will delve into the distinctions between cobot welding and industrial robot welding, shedding light on their unique features and helping you make an informed decision about the most suitable automation solution for your specific manufacturing needs.
Design and Structure
There are some important differences between industrial robots and collaborative robots. Cobots are designed with direct interaction with humans in mind. They have features to ensure the maximal human-robot collaboration in a defined workspace. Not to mention they are more compact and flexible. Their size makes it easy to integrate into existing workspaces compared to traditional robots.
On the other hand, industrial robots are often large and bulky machines used to do the heavy lifting in applications such as packaging and palletising. Designed only for accuracy and speed, industrial robots that are also not force-limited can be hazardous for the human work force.
Safety Features and Considerations
Typically when integrating industrial robots in a workspace, physical barriers, restricted access zones and cages are erected to protect human workers. Any human-robot collaboration is heavily restricted due to safety concerns.
Cobots, however, are specifically engineered for human-robot collaboration. Advanced sensors, force and torque detection, and responsive behaviours help ensure safe interaction with humans. They’re perfect to work alongside humans without compromising safety. The safety standards in place for cobots are designed to ensure that any action the robot performs cannot injure or harm a person, even by accident.
Applications and Industries
Industrial robots and cobots are useful in various industries ranging from welding and assembly in the automotive industry to product inspection, cleaning and hygiene, and logistics. Any task that is typically high-volume and repetitive will have use for industrial robots.
But cobots boast improved versatility, making them more adaptable to a wider range of industries and tasks. Easily reprogrammable, cobots seamlessly transition between smaller batch production, agile manufacturing environments, and dynamic scenarios that demand frequent task changes.
Furthermore, cobots can assist with intricate tasks that demand human expertise, allowing for a blend of human-robot collaboration.
Human-Robot Collaboration and Interaction
Industrial robots operate independently without active human collaboration. Occasionally, there may be operators overseeing the processes but direct interaction is limited due to safety concerns.
Cobots, on the other hand, operate seamlessly alongside human workers. They can perform delicate tasks that require human guidance, assistance, or handling unlike industrial robots.
Programming and Flexibility
Programming industrial robots requires specialised knowledge and expertise. Modifications and reprogramming can be time-consuming and complex, limiting their flexibility to switch between production lines.
With user-friendly programming interfaces, cobots are much easier to program. They allow even non-experts to teach them tasks. Easily reprogrammed and adapted for different applications, cobots can swiftly change between production processes, enhancing flexibility and efficiency.
Cost and Return on Investment (ROI)
Requiring complex infrastructure requirements and specialised programming, industrial robots typically involve significant upfront investment. Not to mention extensive maintenance and reconfiguration, which can quickly add up on your expenses.
Cobots offer a more affordable entry point. Lower initial investment costs and reduced infrastructure requirements are two of them. Being so easy to program and reprogram, cobots contribute to lower labour and maintenance requirements, resulting in a faster ROI for businesses.
Limitations and Challenges
Industrial robots have primarily been used for highly repetitive manufacturing tasks that are hardly modified throughout the lifespan of a manufacturing line. Because traditional industrial robots are inflexible, there are high costs involved in the design and programming effort to integrate into manufacturing lines.
Compared to traditional robots, cobots have limited reach, payload, speed, and accuracy. Unlike their more powerful predecessors cobots have built in limiters that protect their human co-workers and reduce their ability.
Future Trends and Outlook
There are many features that differentiate robots and cobots, but the future of robotics involves continuous advancements in both.
Integration of artificial intelligence and machine learning will play a pivotal role in enhancing cobot capabilities, resulting in heightened intuitiveness, adaptability, and efficiency for every industry. And traditional industrial robots will still be necessary for certain industries.
Overall, manufacturers must carefully consider their specific needs, the difference between robots and cobots, and their industry requirements. While industrial robots have been the trusted workhorses of the manufacturing industry for decades, cobots offer the promise of better efficiency, safety, and productivity.
Our dedicated team of robotic engineers is well equipped to provide you with expert guidance and support, ensuring a seamless integration that meets your unique requirements.
Contact Cyber-Weld now and unlock the potential of cobots in your operations.